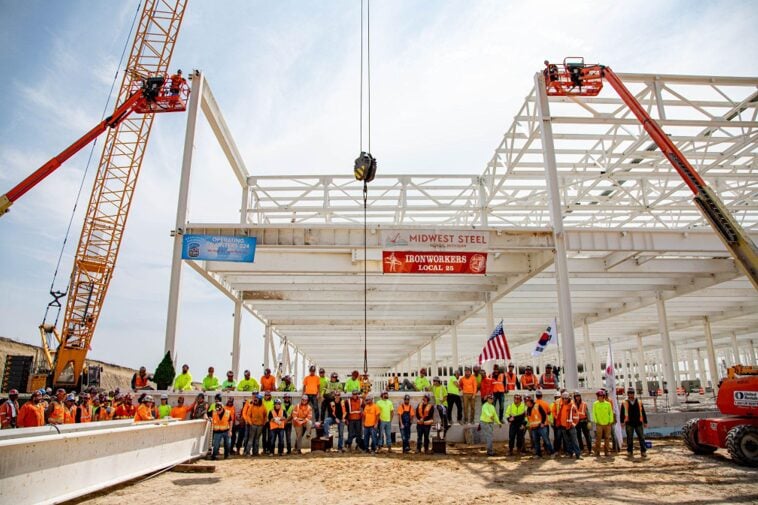
ESN Premium’s two-part interview with the CEO of LG Energy Solution Vertech continues, covering topics such as US customer demand and the Moss Landing fire.
According to Jaehong Park, CEO of LG Energy Solution Vertech (LG ES Vertech), parent company LG ES’s addition of 16.5GWh annual production capacity for battery energy storage system (BESS) cells from its Michigan, US, factory complex this year is “just the beginning” of the company’s capacity expansion.
Enjoy 12 months of exclusive analysis
- Regular insight and analysis of the industry’s biggest developments
- In-depth interviews with the industry’s leading figures
- Annual digital subscription to the PV Tech Power journal
- Discounts on Solar Media’s portfolio of events, in-person and virtual
Or continue reading this article for free
He hints at another big announcement this year regarding BESS cell production in the US. Since the first part of this interview was published, LG Energy Solution has also confirmed that in Europe, it will supply cells manufactured in Poland to a 900MWh project for state-owned energy company PGE.
For LG ES—and others, including Tesla—a trade-off is being made to best utilise production capacity between nickel manganese cobalt (NMC) batteries for electric vehicle (EV) customers and lithium iron phosphate (LFP) for ESS applications.
BESS assembly sites split to cater for US regional demand
In last week’s instalment, Park discussed the adaptations required to repurpose from one cell chemistry and market segment to another.
He says that LG ES is leveraging the capital-intensive investments already put into establishing the factory complex in Holland, Michigan. So, too, the work done to acquire land, get the factory permitted and hooked up with water and other utilities.
However, that still leaves the question of where the complete BESS solutions, including packs and enclosures, will be assembled.
Those secondary steps of assembly are “relatively much easier when it comes to the level of complexity” than manufacturing cells, Park says.
“It’s a little scattered compared to the cell manufacturing facility,” which is all integrated into one site, he says.
“A portion of the pack assembly line is in the same complex in Holland, Michigan. Then we have an additional pack assembly line and system assembly container assembly line in Illinois, near the Chicago area. Then we have another container assembly line in Arizona.”
The strategy is that the Arizona line—which is situated close to the greenfield BESS cell factory site LG ES has put on hold—can be the hub to serve customers on the US West Coast.
The Illinois lines can serve the East Coast and the South, and the site in the Chicago area was selected because LG ES already has a “huge warehouse and logistics hub” nearby, accessible to main arterial roads across the country.
“So, we will mainly operate two hubs for container assembly and pack assembly, but some portion of the pack assembly will be in-house in the Holland, Michigan factory,” Park says.
California’s CAISO not the only game in town anymore
LG ES Vertech was set up by LG ES to capitalise on the growing demand for large-scale BESS in the US. Research firm Wood Mackenzie has just forecast that 15GW/48GWh of energy storage will be installed in the country in 2025, the majority of which will be in the large grid-scale or utility-scale market segment.
While policy uncertainty is weighing heavily on the thinking of many in the clean energy industries. Wood Mackenzie sees a potential for a 22% reduction in energy storage demand between 2025-2029 based on what happens next with tax credit incentives, for example.
As mentioned in the previous part of this interview, Jaehong Park claims however that the full output of the Holland BESS cell factory is sold out for the next three to five years.
As reported by Energy-Storage.news, publicly announced deals for LG ES Vertech include a 7.5GWh supply agreement with Excelsior Capital and an 8GWh agreement with Terra-Gen, as well as an investment partnership with fellow Korean company Hanwha Group’s Qcells.
“We see extremely diversified locations when it comes to project sites,” Jaehong Park says.
In addition to the three already announced deals, more will be announced in the coming months, although they can’t yet be disclosed, he says.
What he can say is that “there are significantly more projects outside of California now,” whereas just a few years ago, almost all of the attention was focused on the West Coast leader in solar PV and, subsequently, energy storage.
“The wave was from the West Coast, and then there was the ERCOT market in Texas, and then it’s moving toward every place, the north, mid-north and East Coast and southeast.”
The portfolio of orders received to date is around 60% outside of California, he says, although with 40% of orders, the Sunshine State still represents LG ES Vertech’s biggest market.
Park’s comments chime with those of Tao Kong, managing partner of renewables and storage developer Luminous Energy, who, writing in a Guest Blog for Energy-Storage.news published yesterday, also said the market is diversifying from its almost-exclusive focus on CAISO in California and ERCOT in Texas.
Though Wood Mackenzie’s latest US Energy Storage Monitor report found roughly two-thirds of all grid-scale deployments in the previous quarter to be found in those two regions, the research firm, too, noted a significant growth in project numbers in 11 other US states.
Moss Landing: Policy, regulation and tech needed to play roles in fire safety
LG ES hasn’t only been in the news headlines this year for positive reasons. The ‘elephant in the room,’ about which it would be remiss of ESN Premium not to ask Jaehong Park, is the large fires at Moss Landing Energy Storage Facility.
The 300MW first phase of what was once the world’s biggest BESS project was destroyed in the incident, setting off a wave of concern among communities and local authorities worldwide. MOSS300 was equipped with NMC cells provided by LG ES and housed in the company’s TR1300 portable racks, although the company was not the system integrator.
Much has been written on that incident and its resultant impacts on the industry. Jaehong Park says that at this early stage, there is not much he can say about the fires. LG ES is “working closely” with Vistra Energy, the project’s owner—which has just written down the value of the project by US$400 million.
“The first priority is to manage the site safely and make sure that environmentally, it is okay. Based on the short-term analysis, the result was good. The air was okay, the soil was okay, and the water was okay. We are working on the long-term impact as well,” Park tells ESN Premium.
“We will come up with some more details sometime soon, but the root cause analysis is under investigation. After the event, we had a stakeholder meeting, including many customers, suppliers and state governments,” Park says.
He claims the stakeholders are “all on the same page” that if a thermal incident does occur at any site again in future, the right regulations, policies and technologies need to be in place to mitigate the risk, to ensure it does not propagate and escalate a thermal runaway into a major fire.
He says many lessons have been learned from experience to date, noting that when the grid-connected BESS industry was getting started, “there was no regulation at all.”
“We just developed what we needed to develop. Later there was UL9540 and NFPA 855, then Fire Codes and Building Codes got involved.”
That evolution continues, with the coming of large-scale fire testing (LSFT). Several BESS manufacturers and integrators have carried out LSFT voluntarily, but it will become a requirement from the 2026 edition of NFPA 855.
“The recent projects that we already deployed are all complying with the large-scale fire test protocol. LSFT protocol means that we burn one single entire container with fully populated batteries inside and then see where there is an explosion or fire propagation to the next containers. There shouldn’t be an explosion; there shouldn’t be propagation.”
Once modular system designs become standardised, and LSFT becomes mandatory, the risk of any incident affecting more than one container on a site becomes minimal, which is the direction the industry needs to go in, Park says.
LG ES sees weight as limiting factor to energy density increases
Finally, speaking of the directions the industry is taking, we ask Jaehon Park for his views on the growing focus on increasing energy density and the corresponding numbers of OEMs producing much larger format battery cells.
“There are a lot of companies, especially in China, that came up with 500Ah and 1000Ah cells because of the density, but I think that now, the focus is not on the density for pouch-type cells [for us].”
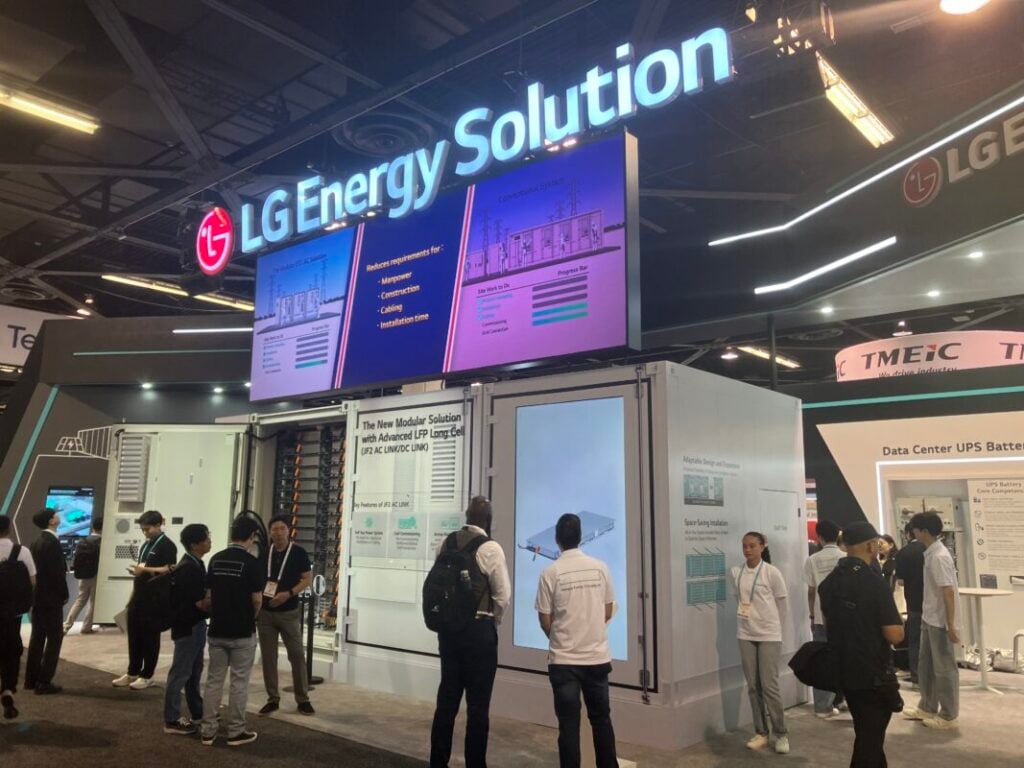
Park says that LG ES is working on a 60A cell, which is roughly equivalent to 300Ah-320Ah, around double that of a prismatic cell.
“I think that’s quite enough. If you look at the enclosure now, the system is modular and fully populated. It has completed the factory acceptance test (FAT) and is then shipped to the site. But there’s also regulation when it comes to transportation. You must be at less than 40 tonnes or thereabouts; otherwise, you cannot transport an enclosure. You need an escort, and you need a special permit to carry such heavy containers,” Park says.
“It’s not a matter of the higher ampere-hour cell. In terms of technology progression, it’s a matter of how we can reduce the weight so that we can have more capacity within one container. LFP technologies in containerised solutions [on the market] are all very similar, at roughly 5MWh to 6MWh capacity, but going forward, the key is how to reduce the weight density. MWh per pound, or MWh per kilogramme, is an important topic from the technology perspective, and it’ll be the next wave of technology innovation.”