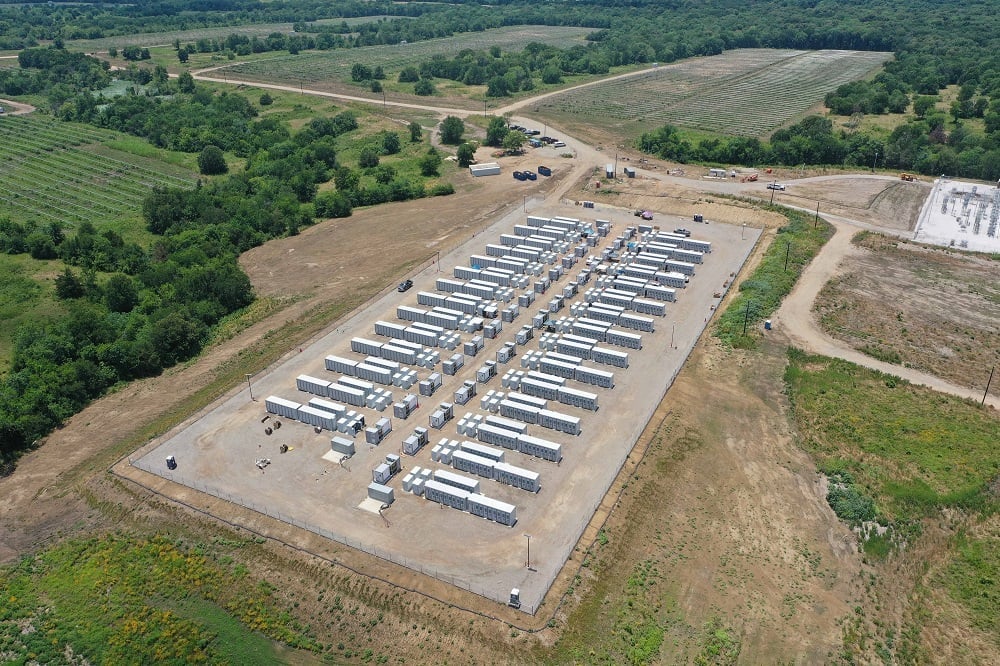
ESN Premium discusses the ongoing adaptation of EV battery lines to stationary storage applications with Jaehong Park, CEO of LG ES Vertech.
South Korea-headquartered battery manufacturer LG Energy Solution confirmed that some of the company’s electric vehicle (EV) cell production lines in the US were being repurposed to make energy storage system (ESS) cells with a regulatory filing in late February.
Enjoy 12 months of exclusive analysis
- Regular insight and analysis of the industry’s biggest developments
- In-depth interviews with the industry’s leading figures
- Annual digital subscription to the PV Tech Power journal
- Discounts on Solar Media’s portfolio of events, in-person and virtual
Or continue reading this article for free
The US$1.4 billion decision to invest in retooling lines at the manufacturer’s plant in Holland, Michigan, had long been expected. In LG ES’s financial results release for 2024, made in January, company leadership had said switching production between EV and ESS based on market demand was a key part of its strategy for this year.
This built on insights into that strategy of balancing production capacity utilisation that ESN Premium had heard about a few months prior from LG Energy Solution’s head of ESS batteries, Hyung-Sik Kim, and Jaehong Park, CEO of its US energy storage system integrator subsidiary, LG ES Vertech.
This also came after the surprise announcement that LG ES was not going ahead with constructing a new-build ESS battery factory in Arizona, although plans were said to be put on hold rather than cancelled entirely.
LG ES had hosted Arizona state officials for a site visit just a few months previously, claiming that it would begin hiring thousands of skilled workers in the second half of this year.
It would have been LG ES’s second standalone manufacturing complex in the US, along with the existing plant in Michigan, with 16GWh annual production capacity for cells destined for stationary battery energy storage system (BESS) projects.
Jaehong Park tells ESN Premium the reconfigured plan will still see that production capacity added in the US—or rather a slightly higher 16.5GWh production capacity as things stand—before the end of 2025.
“I’ve been there a couple of weeks ago with some of the customers to have a tour of how the progress looks. There are some sample manufacturing processes [taking place],” he says.
“We are at the very end stage to complete the manufacturing process and then start BESS production from April this year.”
The facility has three ESS manufacturing lines, each with an annual capacity of about 5.5GWh. The first comes online in April, and the next two follow in June and August.
Park claims that orders for the full capacity of the lines’ output is fully booked by US large-scale project developer customers for the next three to five years. There are plans to add more capacity, although the CEO is unable to reveal details at this stage.
Adapting lines for ESS
So, the reasons for repurposing from EV production to ESS are apparent, based on the slowing growth in demand for one and the acceleration of demand for the other.
Demand for energy storage keeps growing, Park says, especially as successive governments under Biden and now Trump have pursued a ‘Made in America’ domestic content strategy. The growth of AI data centres and the commensurate electricity demand provide further impetus for the deployment of batteries.
Separate factory facilities at the Holland, Michigan, plant will continue making cells for EVs. Still, Park says that LG ES is in an “extremely fortunate” position to be able to adapt lines for e-mobility cells at the complex’s second factory unit for energy storage.
So what does it take to adapt those lines? An obvious difference between EV and ESS battery technologies is the continued reliance on nickel manganese cobalt (NMC) cells for cars while stationary storage systems today are almost exclusively equipped with lithium iron phosphate (LFP) cells.
Jaehong Park says that NMC and LFP chemistry cell manufacturing processes are actually very similar. In that regard “there are not many major renovations required.”
More significant, he says, is the design of the batteries. EV batteries might be expected to perform 1,000 cycles over their lifetime because cars are typically charged two or three times a week.
Conversely, stationary storage batteries will be expected to perform perhaps 7,000 cycles over a 20-year lifetime.
This is reflected in the need for battery storage cells to feature more electrodes, which in LG Energy Solution’s designs have “many stacks inside them,” although “fortunately, we have many electrode lines, so it wasn’t a big deal,” the LG ES Vertech CEO says.
The “one major renovation,” to the factory was related to the fact that ESS batteries are of much larger capacity, necessary to cope with degradation over years of cycling and high throughput.
Why the Arizona gigafactory is on hold
Park says the Arizona plant was put on hold despite its advanced stage of development due to two factors: timing and cost.
“When it comes to timing, if a company builds a factory from scratch, from a greenfield facility, it takes a minimum of three to four years because it requires permitting, it requires water and utilities, and it requires road access.”
“It’ll take a really long time,” versus retooling an existing plant, he says.
In terms of cost, Park estimates that EPC costs for such a project have “probably more than doubled” since before the COVID-19 pandemic due to inflation.
“From the economic perspective, it really makes sense to rebalance the existing facility, rather than building everything from scratch.”
Investing in the battery storage ‘megatrend’
Before the US presidential election last year, Jaehong Park told ESN Premium that the adoption of clean energy is a “megatrend” which will continue regardless of which party holds power.
In our latest conversation, Park doubles down on that view and says LG ES “will keep investing in the US.”
“We already decided to build a factory in the United States and there are multiple reasons why. One, we thought that securing the supply chain, is so important, and then building a local factory really increased the certainty of the delivery. Then, we were so lucky that after we already decided to build a factory the Inflation Reduction Act (IRA) kicked in and that’s been a really great advantage for us,” the CEO says.
He says that building domestic battery production capacity is essential for the US and that batteries will be a vital contributor to energy security.
“Then, if you look at the electricity load growth, going forward, I don’t think conventional technology can catch up with the level of load growth rate. The only feasible solution is renewable-plus-ESS to address those peaks growing every year.”
In the next part of this interview article, to be published next week, we discuss LG ES’s strategy towards battery pack and BESS enclosure assembly. We also get some colour on deals LG ES Vertech has in place as a system integrator in the US and the company’s approach to safety as it responds to the Moss Landing Energy Storage Facility fire.